Made Paper, Made Man
Last week, my "apprenticeship" resumed at Magnolia Paper, a part of Magnolia Editions. After a 3 month hiatus, we're back at it. Don Farnsworth is an iteration engine, rarely stopping, never going back but here we are, doing just that.
As mentioned in the last post, we had cleaned up and painted rust spots on the Noble and Wood beater with bilge paint to eliminate issues with the furnish. At first, it appeared some of the paint was coming off, therefore, an elaborate drying mechanism was constructed of the finest mouldmaking materials around.
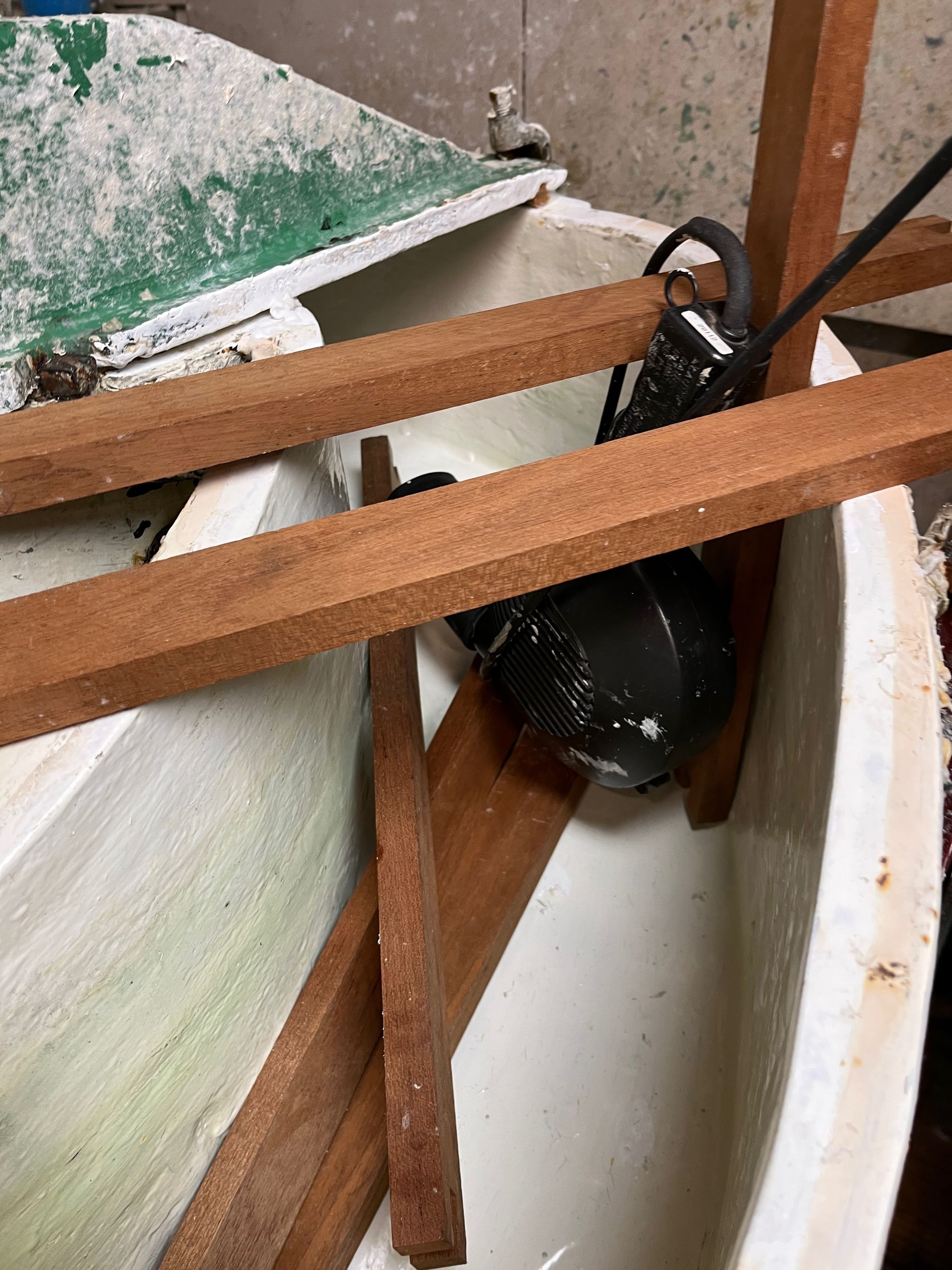
Curing the paint was essential. The beater room was cold, and the paint hadn't completely cured in a week. Localized heat did the trick, though it took repeated applications of this method to achieve results.
I've found that taking breaks from learning rewards me with greater understanding and proficiency upon my return. We had to produce one hundred sheets in a short window, and we worked well together as soon as we began.
I'm new to papermaking, so I don't always know what is coming next and I hadn't been able to anticipate things before we stopped. It was gratifying to be able to pay attention to the needs of the papermaking team, while attending to curing the paint. It felt like we worked in concert far more than before the break.
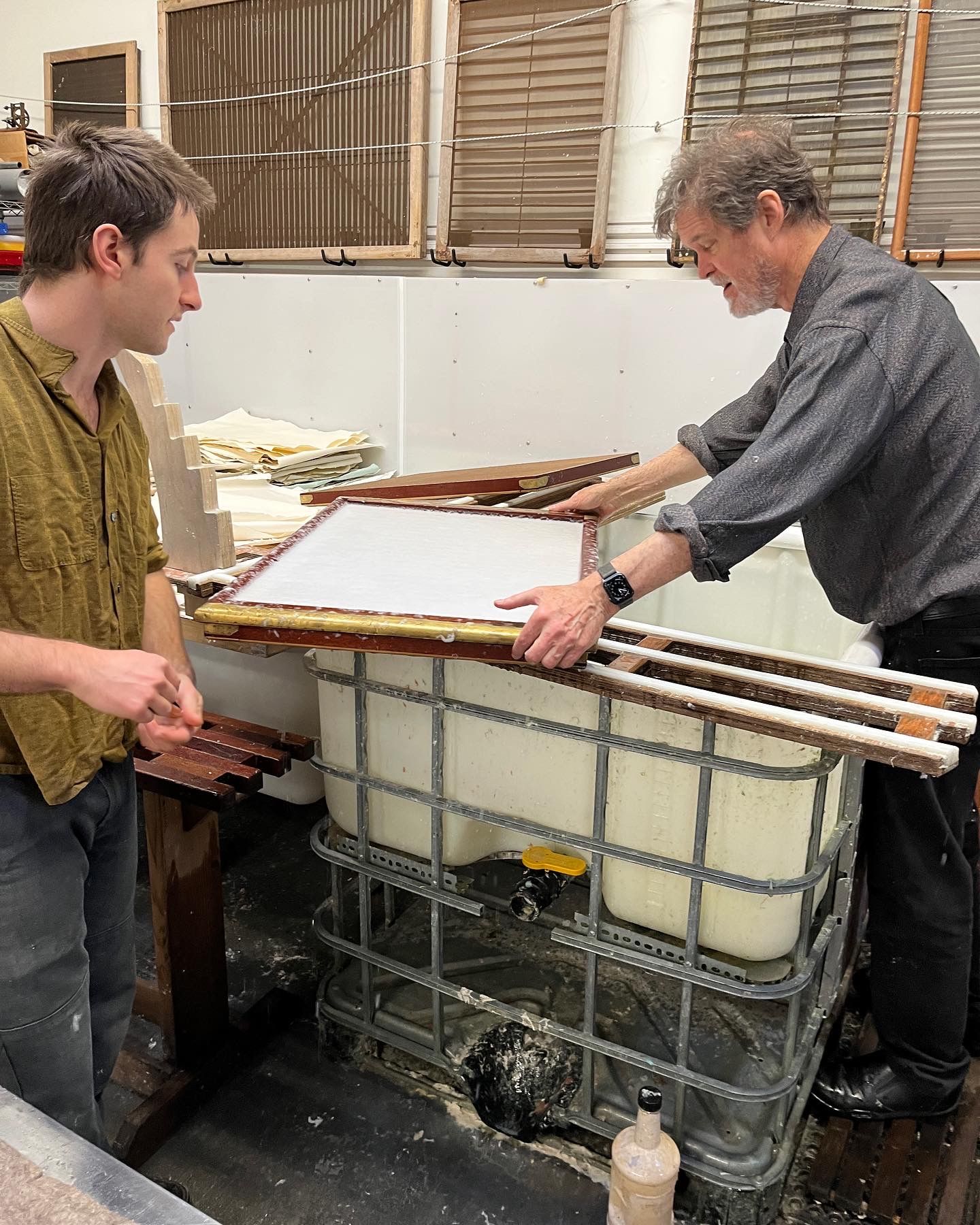
The first day we made about 25 sheets after having set things up in the morning. The second day saw about 46 sheets being made. While forming a sheet of handmade paper seems both simple and magical, it isn't the main activity in the process. It's a bit like being an actor on a stage, or in a movie. Yes, they get to deliver the lines, and they are what the audience sees, however, there's a lot of people and preparation that has to be in place to wow the audience.
That we were able to get the results we did so quickly after stopping for 3 months was gratifying to experience. Getting a project completed quickly meant that we could return to the research-driven experience of solving the evermore-refined questions about Renaissance paper.
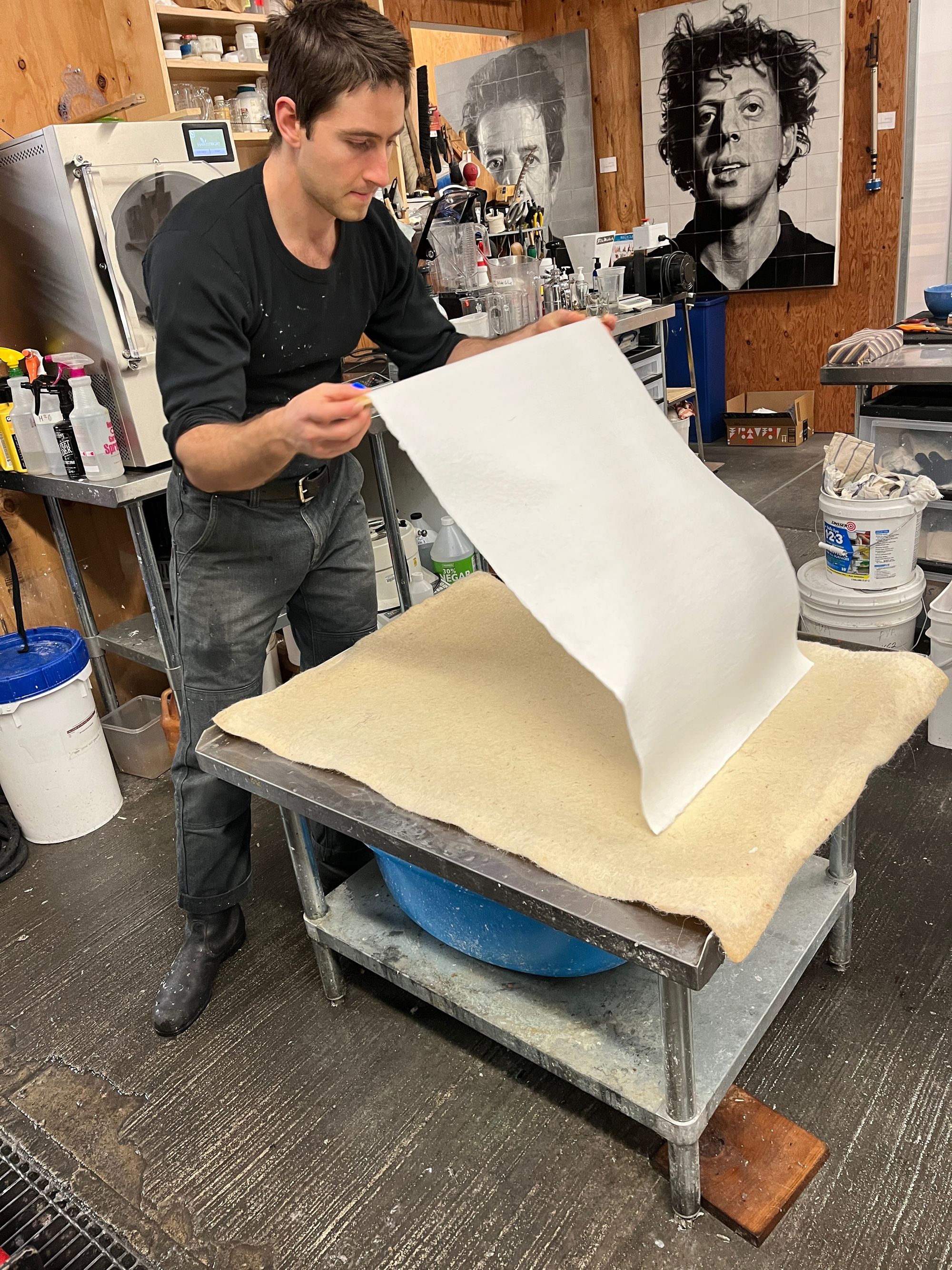
Guy Diehl is part of the testing process to observe how media behaves on the paper. His background in historical methods, skill at rendering with the tools and materials of the Renaissance and early-modern art provide Magnolia with an encyclopeadic knowledge base. I've benefitted from observing and listening to him.
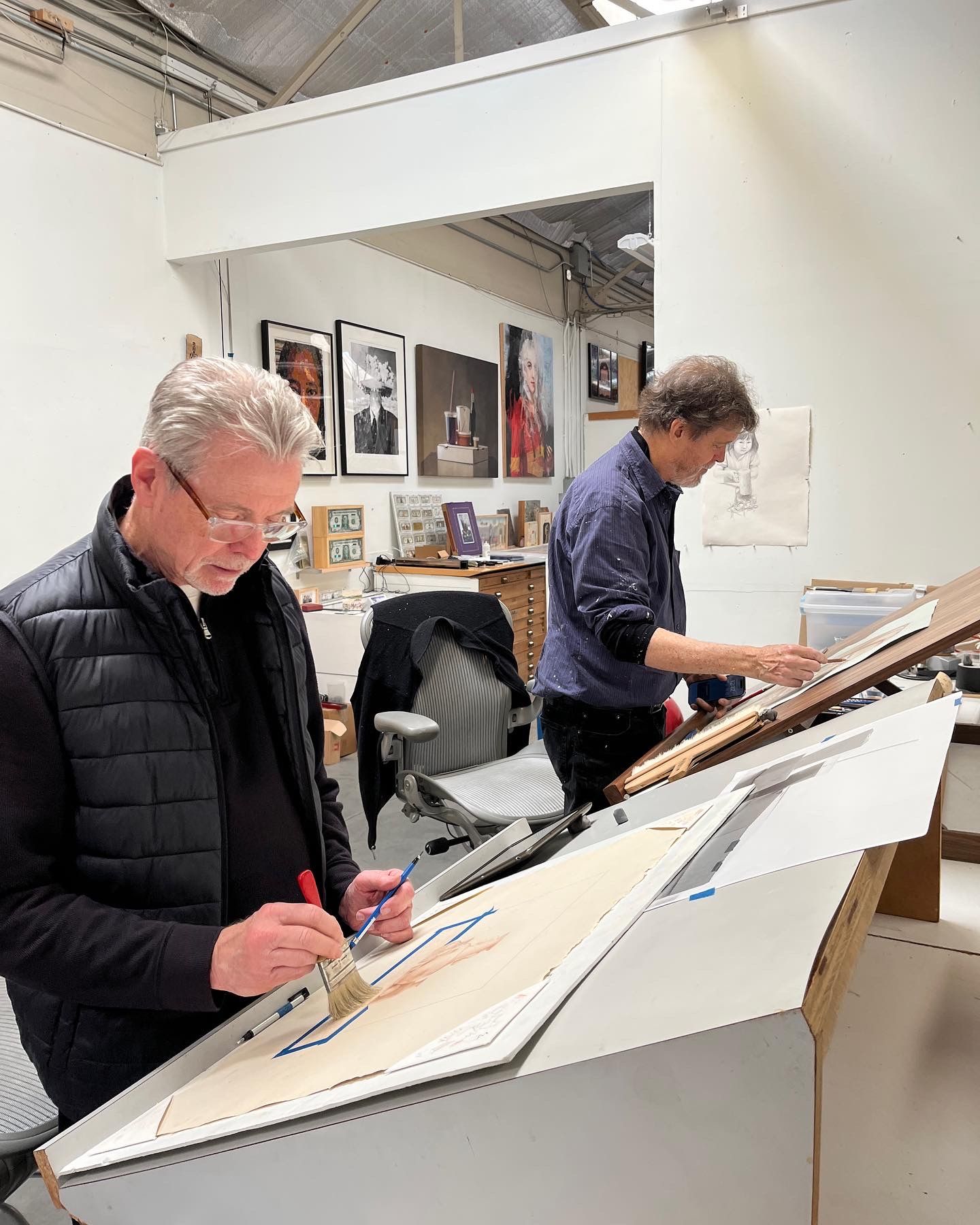
Nicholas Price was working out roasting techniques with the new induction roasting equipment, and a tasting of Kenyan and Mexican beans enlivened the morning routine. Conversations ranged from coffee-making techniques to Nicholas's collection of coffee-making equipment. It's a pleasure to be around people who are comfortable with committing to thier hobbies with passion.
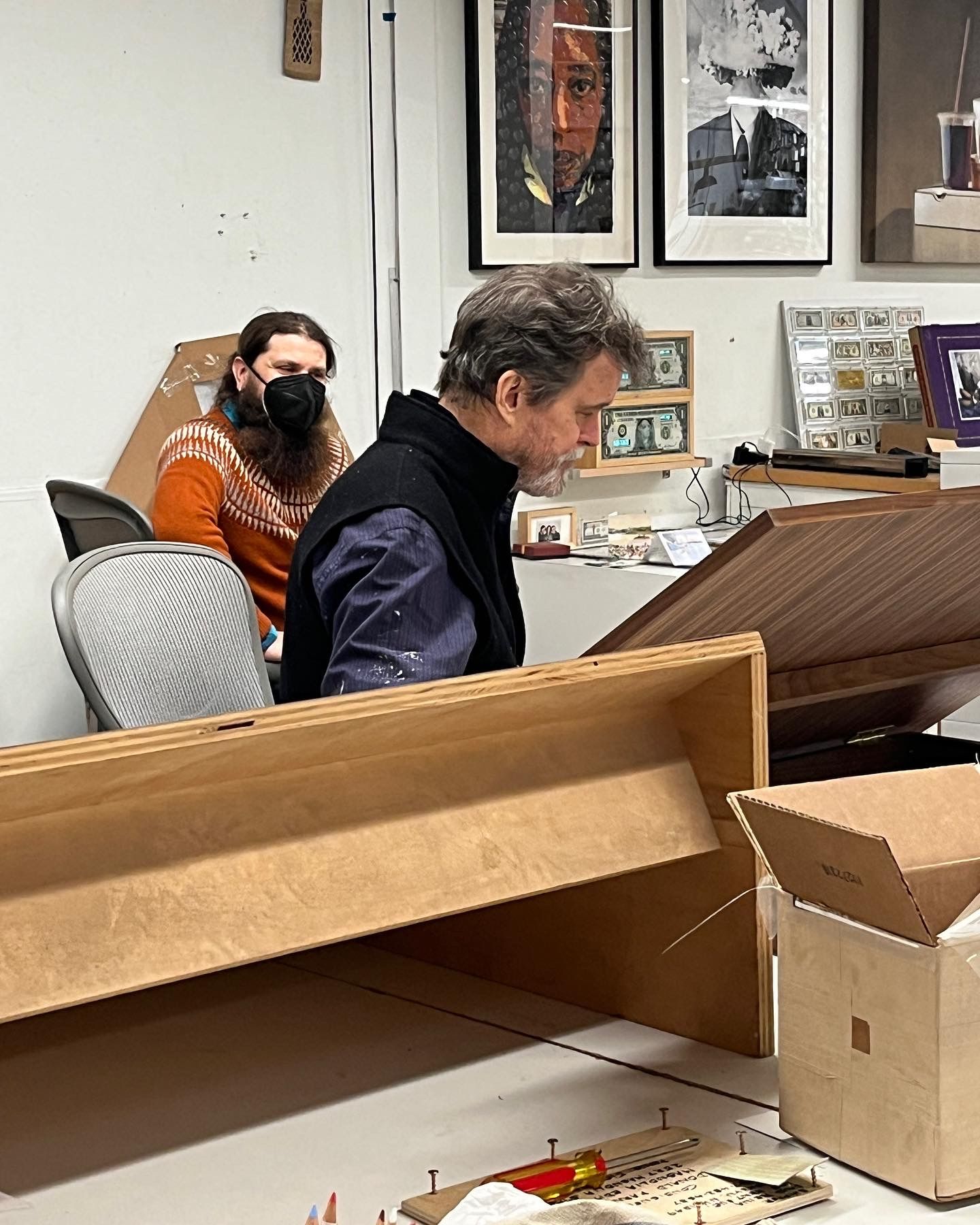
Tallulah Terryll is printing the edition on the flatbed acrylic printer, and has been working with Max Thill to choose the final sheets used in printing. Care and attention is necessary to preparing this paper to be well-printed. Meticulous hair and wool removal from the surface, sizing, and flattening require observation, analysis, and discussion to get the best results.
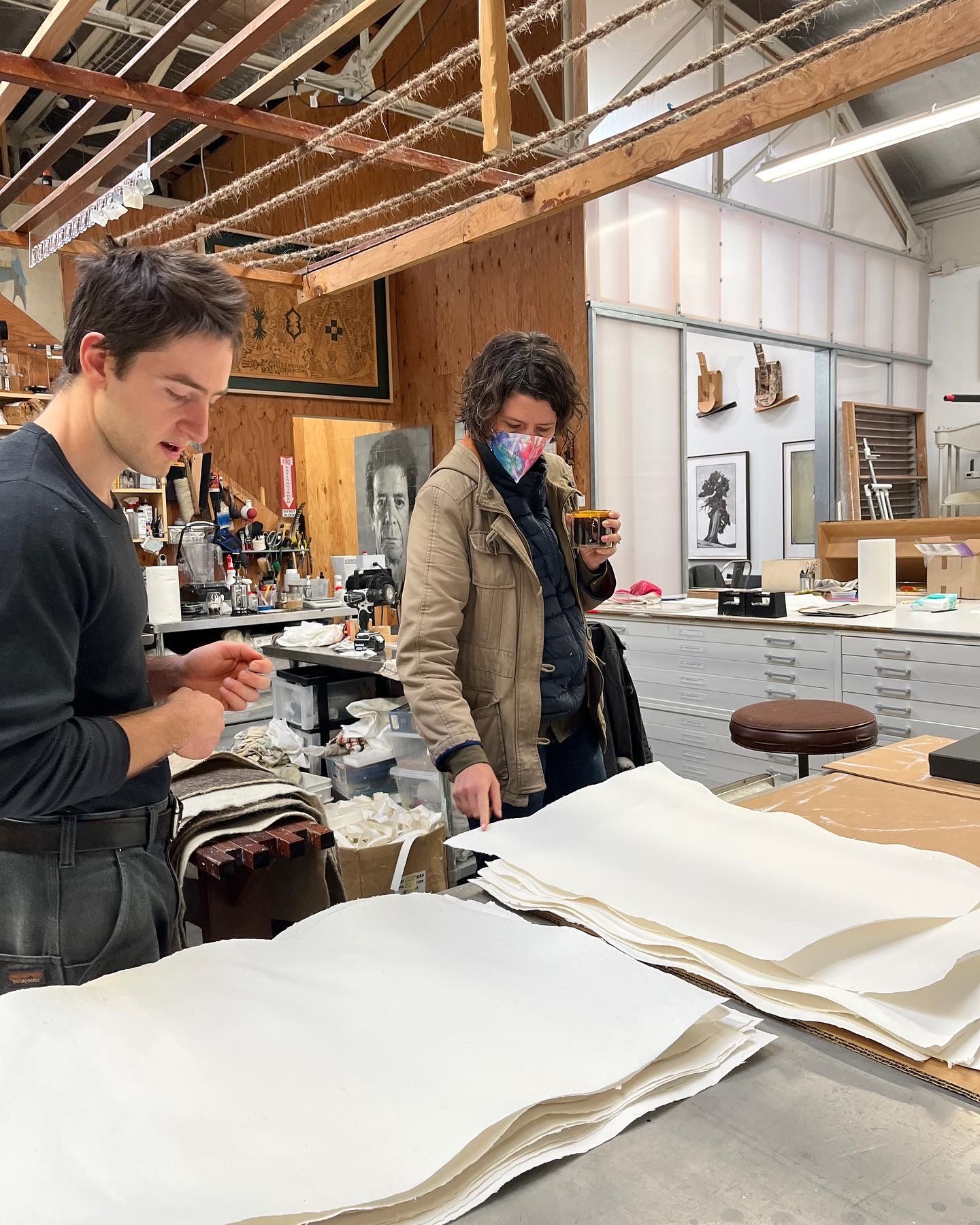
Tallulah Terryll reviews sized sheets with Max Thill during the coffee tasting.
On Saturday, I was able to resume my own papermaking efforts when I beat some lightly pigmented flax in my Valley beater.
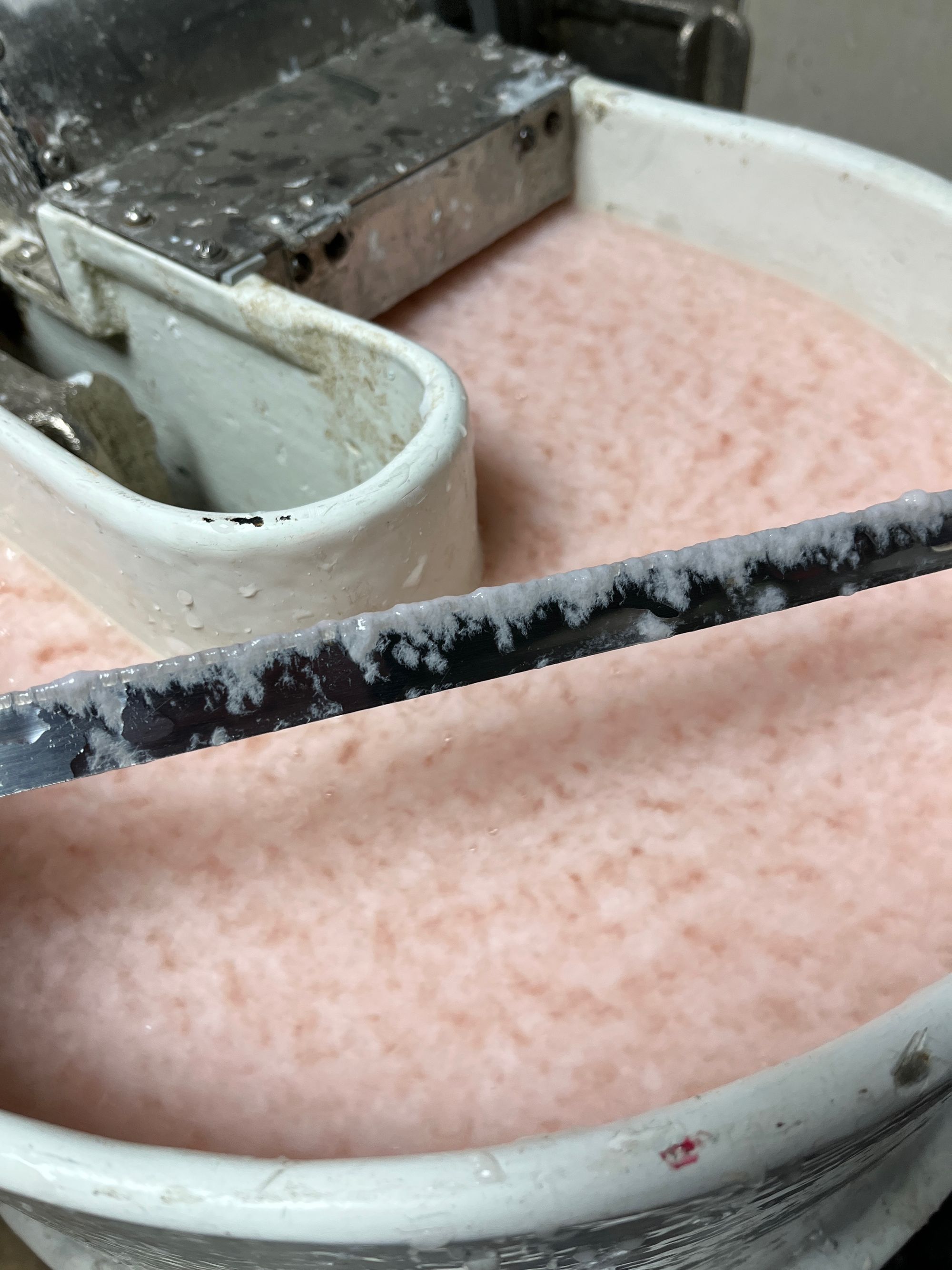
The weather has been harsh around the US, however here in the East Bay, it was beautiful and mild. Cold water to make paper is bracing, but can turn unpleasant if the weather is chilly. I got lucky and had golden light and mild temperatures to work in late in the afternoon.
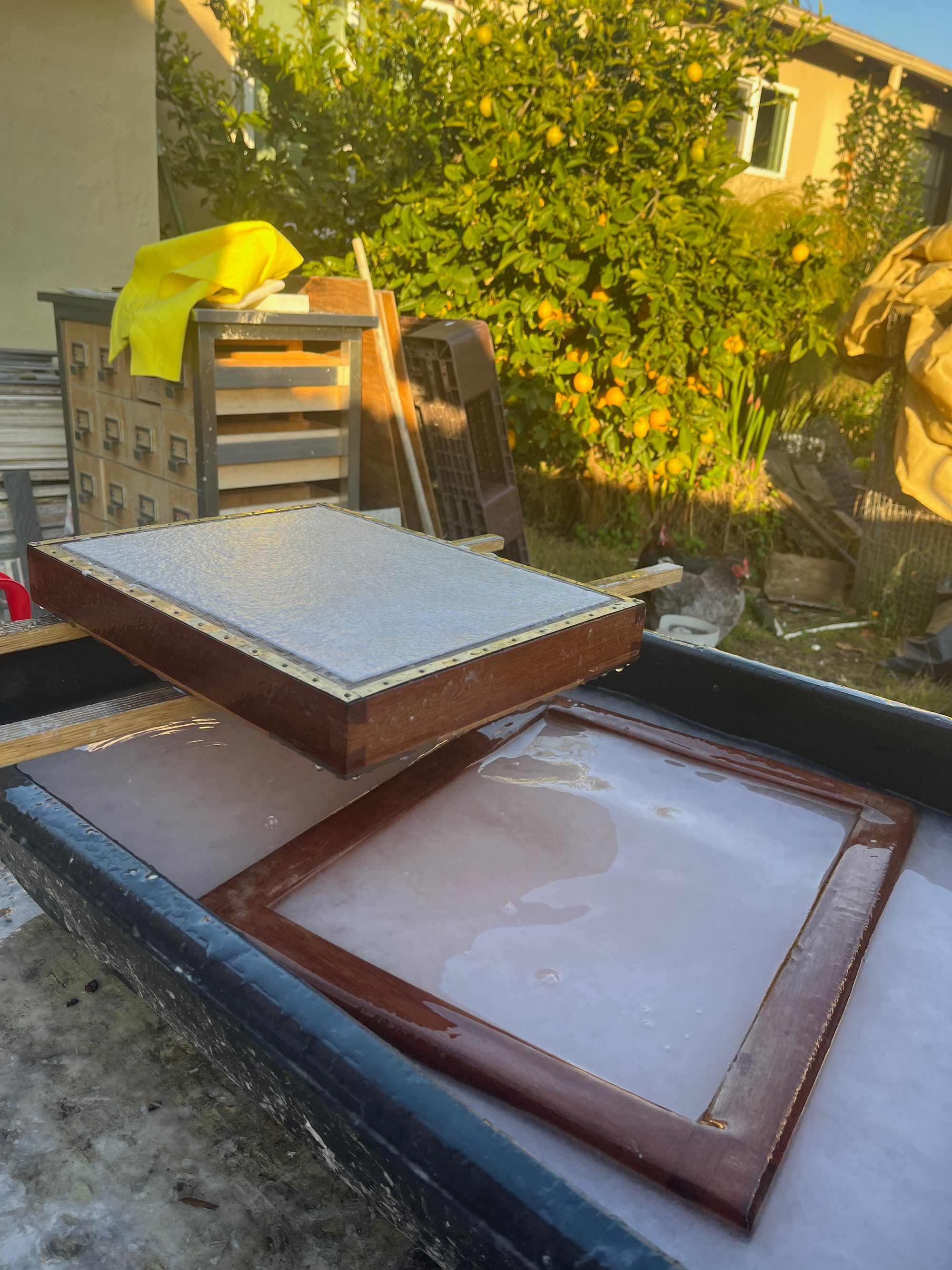
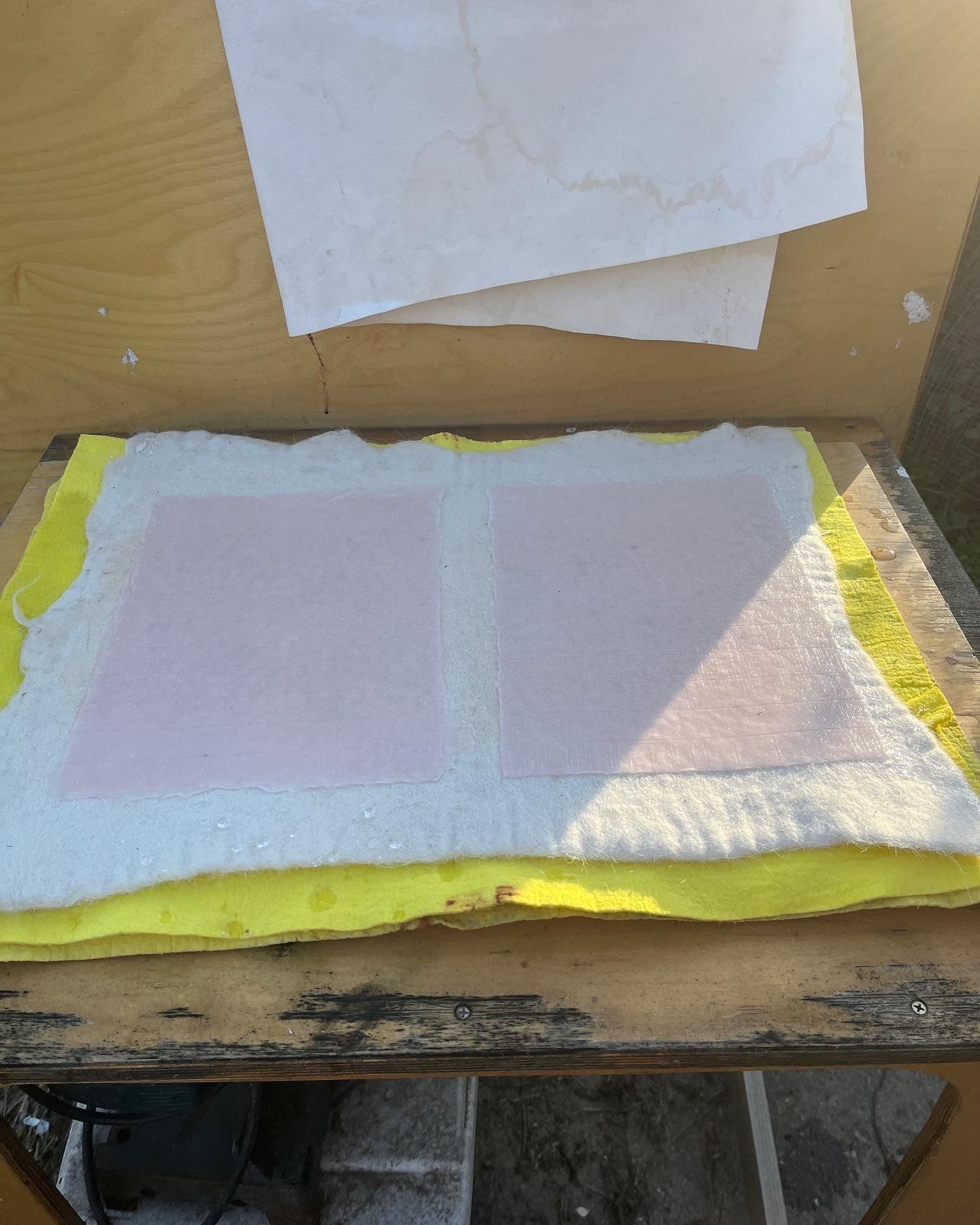
I no longer have a dewatering press, and it was a challenge to get the sheets drained enough for transfer to spurs or the restraint dryer. I'm using water-filled buckets as a press. It's not very effective as a means to do this, but I do what I can with what I have. Water removal is a requirement in proper hydrogen bonding to form, and that's what makes paper "paper." I hope that my next post will show the hydraulic press I have assembled and with platens for use in papermaking.
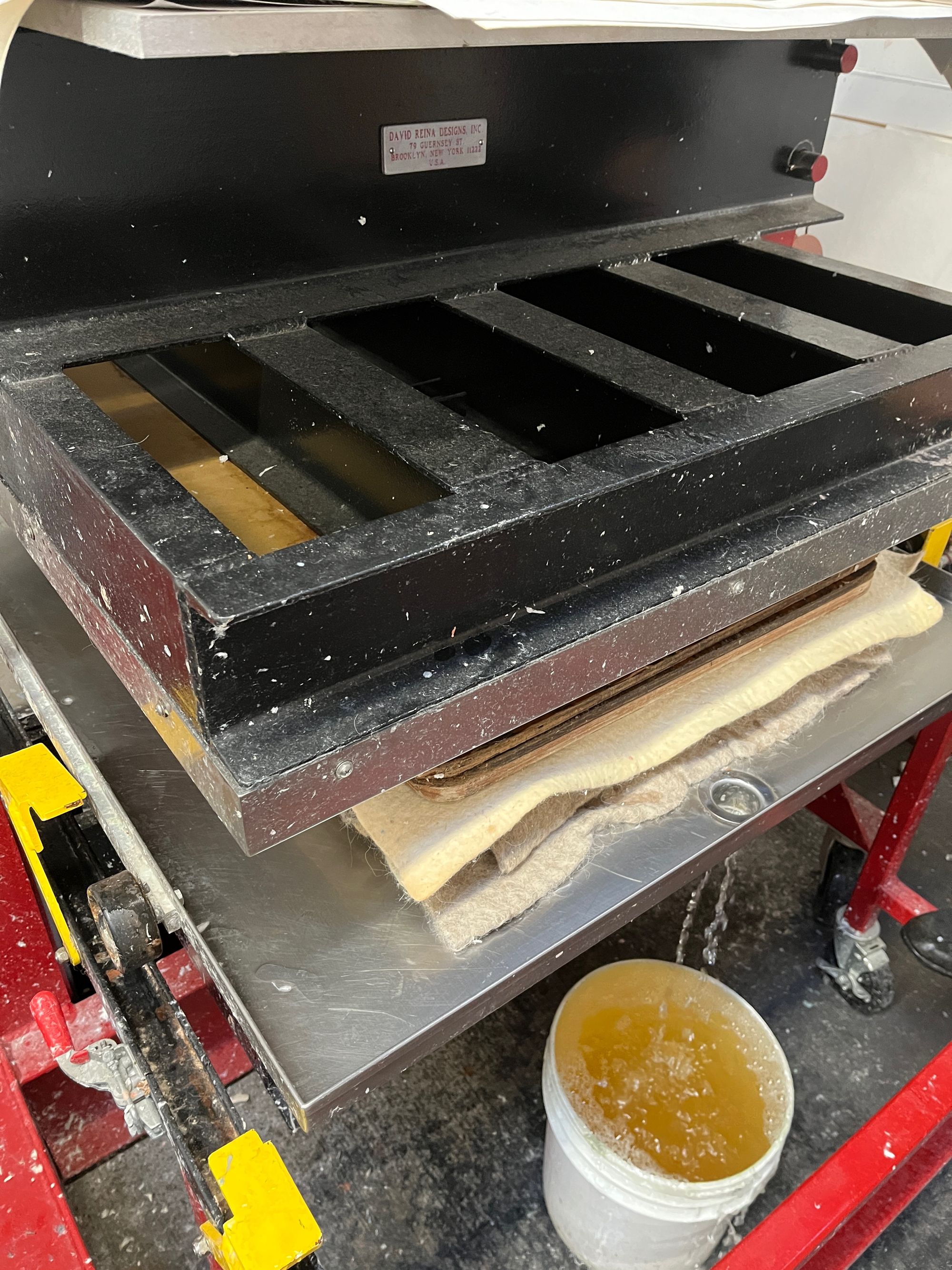
The day ended with my make-shift press. It was insufficient in dewatering overnight, and I found it difficult to lift sheets off the felts, so I improvised and interleaved dry felts between the felts with sheets on them. They're coming out of the "press" shortly, and then I'll move onto drying them. I can tell that my sheet-forming technique has improved since working at Magnolia, and I look forward to increased competence as I make more paper.
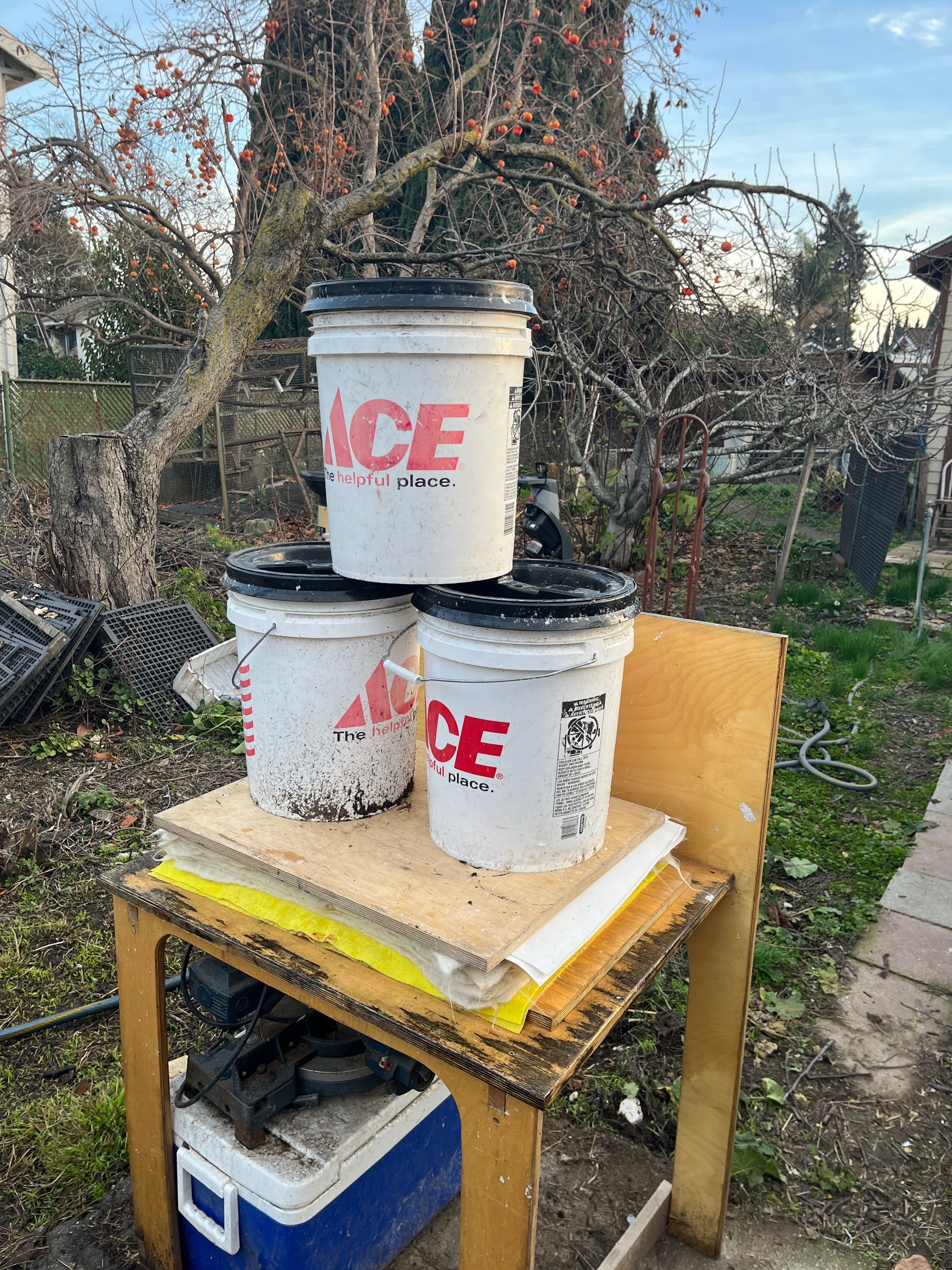
Rain is coming this week, and I make paper outdoors, so I may halt production and design a linocut to print on this paper while the California landscape gets its much-needed winter rainfall.